2015 – 2016, funded by AKB Stiftung
In the recent past years negative environmental impacts due to plastic waste induced by industrial mass production have become visible all over the world and consequently became a global challenge.
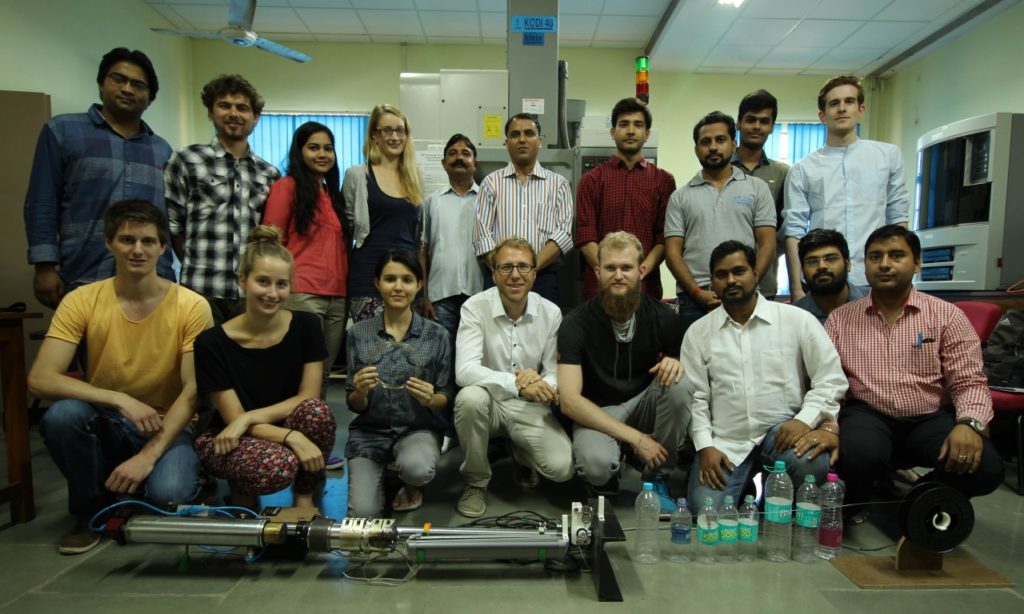
At the same time the demand for personalized products, which are
manufactured to order in small batch sizes, has significantly risen and the impact of sustainability on manufacturing companies driven by customer demand and legislation has increased. Subsequently, products made in a more sustainable way can have an economic advantage over their conventional counterparts.
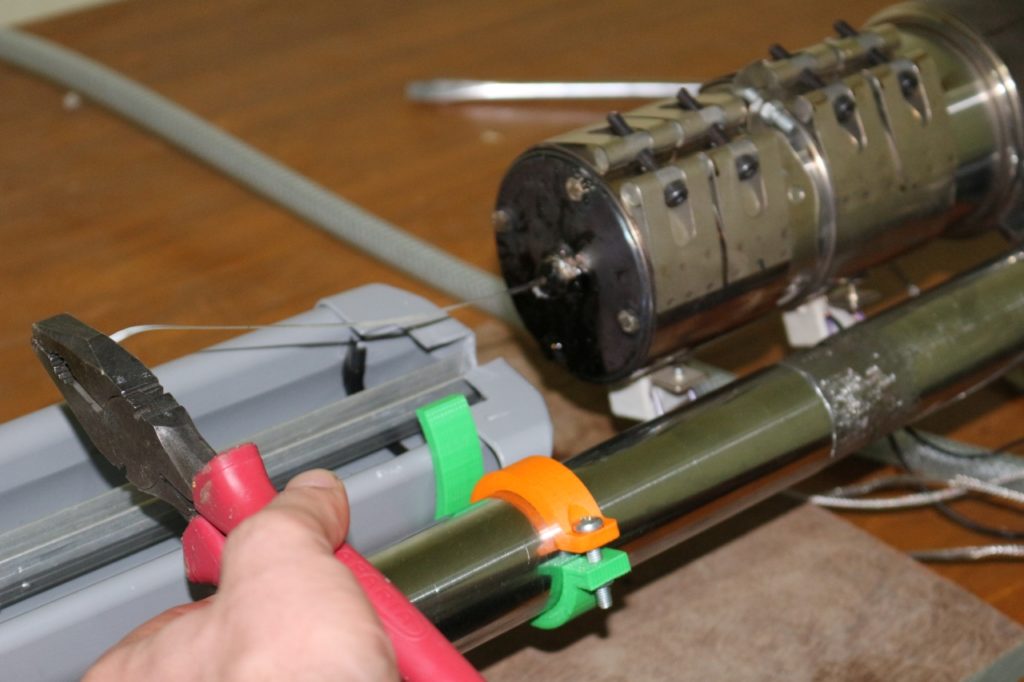
The additive manufacturing technology fused deposition modeling (FDM)—also known as 3D-printing—can be utilized as a production process that can comply with these demands. In FDM 3D-printing a plastic filament is heated and added layer by layer to form a three dimensional object. With this additive production process the material usage grade can be much higher than with conventional subtractive processes as almost only the material is added to the part that is actually required. The production of the basic material for FDM, the filament, has a significant impact on overall costs and environmental impact of the 3D-printed parts. The utilization of filament from plastic scrap material can thus contribute to more sustainable products manufactured by 3D-printing.
In the project “3-Cycle” a small and modular process chain was developed for 3D-printing with filament from extruded waste plastics. Together with researchers and students from BITS Pilani the process development, application, and evaluation took place, both at the Experience Lab at IWF TU Braunschweig and at BITS in 2015 and 2016. The project was funded by AKB Stiftung. In the “3-Cycle” project a great number of students from India and Germany were involved. These students worked individually and in small groups on project tasks mostly during the course of their theses. In total 16 students and several researchers contributed to the design, construction, testing, and evaluation of the recycling process. Two student groups from Germany were able to visit BITS Pilani in June and October 2015, not only learning about plastics, 3D-printing, and recycling, but also about a new perspective on sustainability.
The project results were published at the Indo German Conference on Sustainability 2016 in Chennai. In the learning factory at TU Braunschweig (“Die Lernfabrik”) the recycling process chain is integrated into the Experience Lab. Students and visitors are able to experience the steps from plastic waste to filament from which new products are made with 3D-printers.